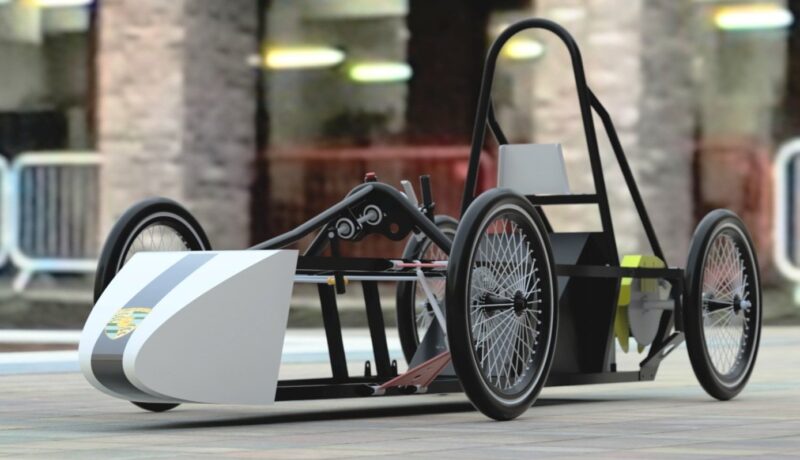
Reverse Engineering the Nose Cone
Greenpower issued a technical bulletin in February 2019 with the purpose of making sure that nose cones were manufactured to ensure safety. As part of this, rule T8.1 had a new process for scrutineering.
T8.1: Anything forward of the bulkhead in T7.1 must be easily deformable.
Unfortunately this results in Blue not being able to pass a scrutineering check. We pleased our case demonstrating the deformability of the nose after the 1.5mm of filler, which gave us grace until the end of the season.
We have a beautifully designed nose cone on White, which had been designed and fitted by the previous owners of the car, but we wanted to be able to recreate this.
Fortunately we had some DXF sketches to work from. Unfortunately there were a number of complex curves we needed to figure out, which the 2D files didn’t help with.
Out came our new 3D scanner!
[IMAGE AND EXPLANATION HERE]
Using the new scans and original DXF files, we were able to get a very very close model to the original in Fusion 360.

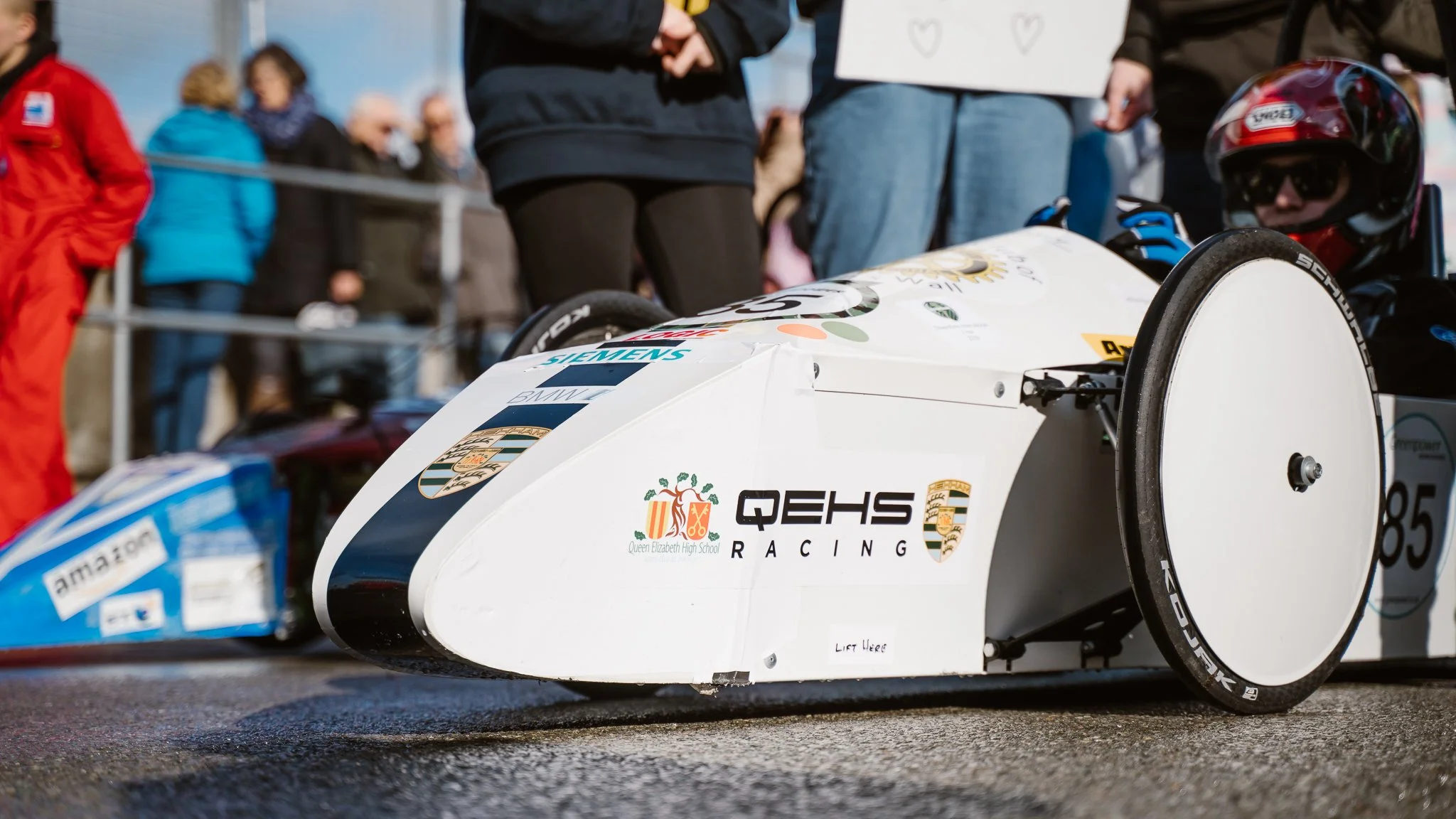
The next issue was a slightly more complicated one. We need to get a flat pattern of this nose to match the curves on the new model. Unfortunately, Fusion 360 isn’t a fan of generating flat patterns for models with complex curves. Autodesk do however have another product, Meshmixer, which is able to do this very well!

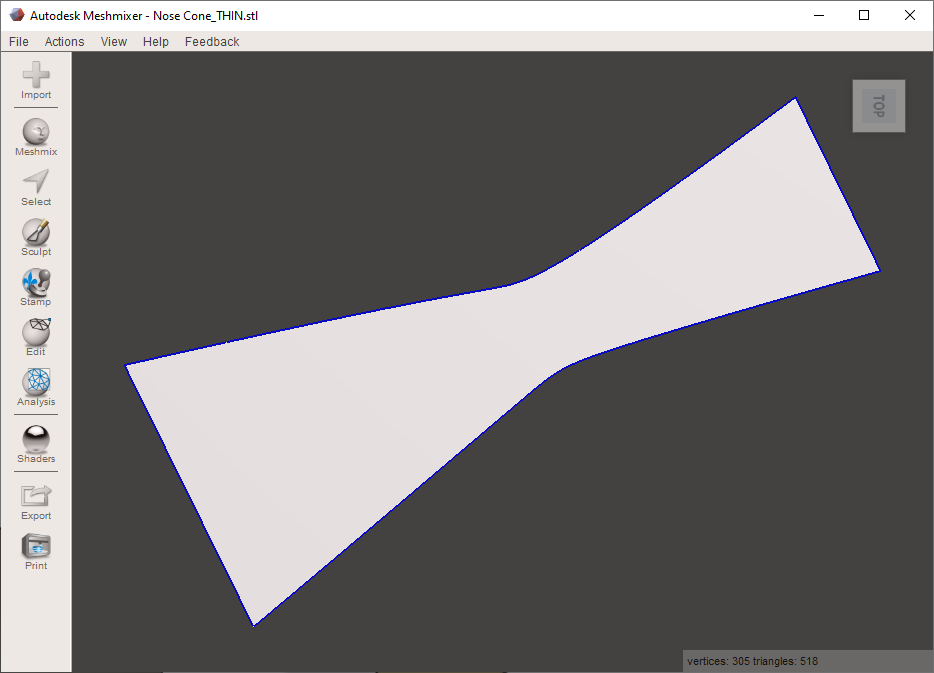
So now that we have flat patterns to recreate the nose, what next? Remember those complex curves from earlier? They’re going to be back to haunt us!
We need to make a jig to allow us to hot-form the ABS into the shape we need. Fortunately, there is an amazing tool called Autodesk Slicer, which will allow us to laser cut and assemble a jig.

And with that, we should be able to repeatedly manufacture our nose cones with ease!